5 Things To Look For When Picking The Right Toolholder For Your Application
- Social Media @ EXSYS Automation
- Oct 20, 2020
- 3 min read
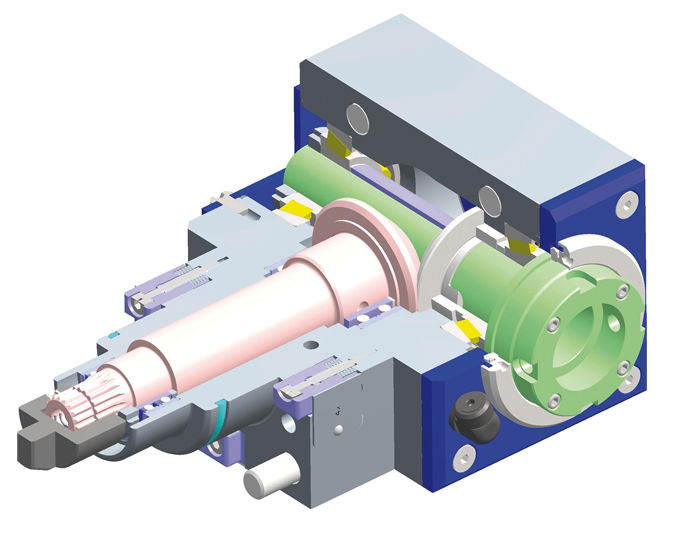
When searching for the right toolholder for CNC machining several things must be taken into consideration when selecting the right holder for your needs, capabilities and applications. Five very important aspects of tooling that increase productivity and the life of the toolholder and machining center are: the housing, bearings, seals, couplings, and presettable or cartridge-based adapter system.
Housing
Many manufacturers use castings, or two-piece housings for their toolholders, which is fine if you’re utilizing the tooling for less-demanding cutting that requires little accuracy and rigidity. A one piece, cold rolled “steel housing ensures reliability, rigidity and stability through the most demanding process.”
Bearings
Angular contact, or ball bearings are commonly used in the industry. The ball bearings when seated in the bearing seat, provides a known tolerance for the ID. These bearing offer high accuracy and high speed, as well as the tapper roller bearing, yet less contact surface. The taper roller bearings provide more contact surface than other bearings, which allows for more rigidity. The taper roller bearing also permits greater side-load and have increased longevity in dirty environments.
Seals
Seals protect the toolholder’s bearings from washout. Lip seals, or oil seals hug the shaft to prevent liquid and light debris from entering the live tool. Although these seals prevent washout, the way they “hug” the shaft creates friction, which in turn creates heat. The labyrinth seal protects the bearings from the operating environment by creating a complicated path for the coolant to follow. Eppinger offers a patented double seal system, which disperses excessive heat and prevents unwanted leaks, while the tool is not only operating, but stationary as well.
Couplings (Drive Dog)
One of the most prevalent drive systems for live tooling is DIN1809, otherwise known as the drive tang. This system is rigid and reliable, but has one down fall; the mill drive and the machine do not always line up to the toolholder. These small misalignments create side load on the drive tang. The side load flexes the spindle and creates vibration. The vibration not only creates heat, but also travels through the cutting tool and is shown in the surface finish of your work piece. “The compensating clutch has the ability to “wobble” allowing for minor misalignments to the turret drive motor eliminating side load, yet still providing increased torque transfer and greatly improved surface finishes as well as longer tool life.”
Cartridge Based Adapter Systems
Cartridge-based adapter systems can lead to greater added value to your turning center tooling; drastically reducing setup time. When multiple setups, and tool and insert changes are required, these systems will help you reap the benefits of reduced setup and tool changing times. Although these adapter system toolholders may cost more initially, the savings in the long run will pay for themselves many times over. Many companies offer their own adapter system limiting the user to only using their adapter systems. Eppinger’s PRECI-FLEX® is the only cartridge based adapter system that has a highly accurate cone-face connection, utilizing the standard ER Collet pocket. This gives the user the option to use the standard ER collet, or the adapter system.
Although there are many things to take into consideration when deciding on the right tooling for your needs; these five important aspects of a live tool’s capabilities can dramatically change the speed, accuracy, and rigidity of your project.